В ТГУ растят детали
ТГУ выращивает детали для тольяттинских автопредприятий. Когда впервые слышишь эту фразу, думаешь: бред. Но все оказалось правдой – именно выращивает.
Тольяттинский государственный университет два года назад выиграл грант по постановлению №219 Правительства РФ на закупку уникального инновационного оборудования. Это позволило вузу приобрести сверхсовременные машины более чем на сто миллионов рублей. Они вывели ТГУ на новый уровень решения конкретных производственных задач. Кто-то удивится: какие такие производственные задачи может решать университет? А вот какие. Благодаря новому оборудованию университет делает детали, необходимые, например, для производства автомобилей по инновационной технологии. И процесс этот, действительно, напоминает «выращивание», которое происходит в чудесном устройстве – 3D-принтере, самом крупном и высокоточном в регионе. Второго такого нет ни у кого. На нем можно изготовить любую конструкцию – от кнопки до двигателя, причем сложность изделия не играет вообще никакой роли. В принтере есть площадка (поле, на котором выращиваются различные фигуры), залитая фотополимером. Включается лазерный луч, который двигается по определенной программе, заставляя фотополимер послойно отвердевать. И вот на глазах ввысь и в ширину растет деталь.
– Мы это называем прототипированием, – рассказывает проректор по научно-инновационной деятельности ТГУ, кандидат технических наук Сергей Петерайтис. – Любой производственник вам скажет: чтобы изготовить изделие, сначала надо сделать мастер-модель, некую эталонную деталь, а потом уже пресс-форму под нее, которая в некоторых случаях стоит до миллиона рублей. И вот представьте, что мастер-модель была неудачной. Миллион выкинут на ветер. Мы эти ошибки исключаем. Новизна технологии, которой мы пользуемся, позволяет весь процесс значительно ускорить и удешевить. На изготовление эталонной модели не требуются огромные затраты. Цена изделий, выращенных на 3D-принтере, составляет на рынке России либо от 60 до 70 рублей за грамм, либо 50-70 рублей за кубический сантиметр. Мы на 3D-принтере выращиваем и доводим изделие до эталона.
3D-принтер стоит первым в технологической цепочке. Второе чудо техники – вакуумная машина, тоже уникальная. Здесь происходит следующий этап работы – изготавливаются силиконовые формы, с помощью которых потом тиражируют различные изделия. Мастер-модель обволакивают силиконом. Полученный параллелепипед разрезают, модель убирают, а форма остается. В ней проделывают прорези, так называемые питатели, через которые потом заливают материал с заданными свойствами, нужными заказчику. Это может быть и пластик, и металл – нержавейка или драгоценный, разницы нет. Удается добиться микронной точности, после которой не требуется никакой дополнительной механической обработки. Ювелирная работа, после которой можно идти в литейный участок. Это особая гордость Сергея Петерайтиса. Ведь «литейка» создавалась под его началом с нуля. Здесь тоже установлено оборудование, закупленное по гранту. Еще год назад делегация из университета ездила на одно оборонное предприятие России, где делают 95 процентов атомного оружия страны. Хотели у них поучиться, но оказалось, что те сами в стадии запуска и до конца некоторые технологические цепочки не освоили.В то же время специалисты этого предприятия приезжали в ТГУ на обучение, так как за год так и не научились лить цветной металл.
– Мы не беремся за тиражи в тысячи штук – мы же не кооператив, нам это неинтересно. Мы – наука. Отрабатываем для людей технологии, доводим конструкцию изделия до товарного вида и предлагаем заказчику, – поясняет Сергей Петерайтис. – Например, для Джи Эм-АВТОВАЗа мы делали партию плафонов для машин, 35 штук. Прежде чем этот плафон довести до реальной конструкции, которую можно было бы на автомобиль поставить, мы только четыре или пять раз меняли мастер-модель. Очень сложная деталь. Там защелки, которые не должны ломаться, должны соблюдаться правильные углы. Мы все это, как правило, дорабатываем, делаем дополнительные расчеты, занимаемся моделированием на компьютере.
На участке прототипирования есть и другие интересные аппараты, например, 3D-сканер. С его помощью можно отсканировать что угодно. Процедура занимает десять минут, и пожалуйста – на монитор уже выведена 3D-модель. Недавно автокомпонентщики из Октябрьска просили сделать карту замерорейлингов на крыше автомобиля. У них особая кривизна, которую не очень измеришь. А сканеру без разницы, какая сложность и какая форма изделия.
Не удивительно, что предприятия автопрома всерьез заинтересовались теми возможностями, что имеются в ТГУ. В сфере прототипирования АВТОВАЗ сейчас ни с кем больше не работает, только с университетом. В автомобилях-прототипах, которые катаются где-то на испытаниях, уже установлены изделия «made in ТГУ». Когда станет ясно, что детали идеально устанавливаются на автомобиль, хорошо эксплуатируются, завод уже сам изготовит под них пресс-форму и начнет тиражировать готовые изделия тысячами. ТГУ в этих взаимоотношениях выступает как опытное производство, которое позволяет довести изделие до конвейера с меньшими затратами. Как тут не сказать спасибо инновационным технологиям! Только за этот год Тольяттинский государственный университет заключил три договора с автозаводом. Первый – по изготовлению впускной системы для двигателя, второй – по изготовлению 25 элементов салона и наружного пластмассового обвеса, третий заказ, который выполняется сейчас – модернизированная выпускная система для автомобиля. Аналогичная работа на оборудовании Инновационно-технологического центра госуниверситета (ИТЦ ТГУ) была выполнена весной этого года и для Джи Эм-АВТОВАЗа.
– Сегодня наш университет активно включается в процесс преодоления трудностей промышленной сферы и ведет «агрессивную» политику по внедрению своих инноваций на рынок, по организации диалога и постоянного сотрудничества вуза с промышленными предприятиями, – говорит Сергей Ханцасович.
Буквально на днях ТГУ подписал соглашение о научно-техническом сотрудничестве с еще одним предприятием – Тольяттикаучуком.
Елена Харченко
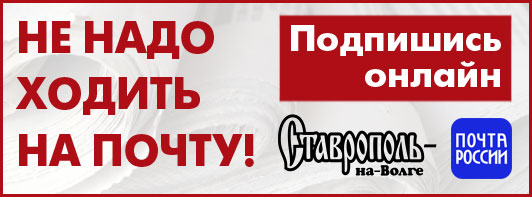